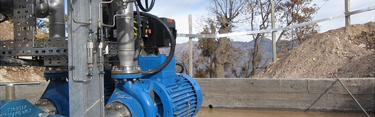
Additive solutions
We help organisations processing industrial liquids and gas to manage additive injection and pressurisation through the design and manufacture of tailored skids. Our systems are custom-engineered to the highest standards to ensure accuracy, reliability and regulatory compliance when it matters most.
Our in-house design and manufacturing ability, engineering knowledge and technical expertise set us apart from the competition and allow us to react quickly and efficiently to the needs of our customers.
As an independent systems integrator, we have access to products from leading industry suppliers and will always select the technology best suited to your application.
- Skid-based solutions reduce time on site making the project cheaper, safer and more convenient.
- Pump skids for the pressurisation of additives, hydrocarbons and chemical liquids.
- Standalone systems inject one or more additives into a product line.
- Loading rack-mounted injection systems are found in the majority of fuel terminals.
- Turbine-driven Injection Systems deliver accurate self-powered additive injection.
- Dual-pumping technology operates the pumps alternately to extend their life and build in pump failure.
Added value
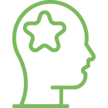
Expertise

Partners
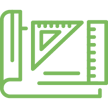
Design
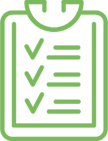
Testing
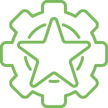
Services
By combining our depth of knowledge with a forward-thinking engineering team, we continue to confidently deliver new and innovative solutions.
The additive solutions we design and manufacture offer a wide variety of component options. Each system is engineered to suit the users’ current and future additive requirements and to incorporate additive storage, pressurisation and monitoring equipment such as temperature, pressure and flow transmitters.
At Flotech our philosophy is to complete as much of the build off-site as possible by delivering a skid-based solution. The advantages of this approach include;
- The system can be piped, cabled and flow tested in advance of delivery.
- Snagging is done off-site which minimises site assembly and start-up time.
- Large skids can be built in modular form to allow road transportation.
- Reduced time on site makes the project cheaper, safer and more convenient.
- All welding, assembly and testing is performed at our fully fitted facility in Hampshire. Quality is assured since all welding, pipework and assembly is performed by qualified and experienced personnel.
Additives we build systems for include:
- Performance enhancing additives
- NoX reduction additives
- Marker Dyes
- Anti-static additives
- DNA Markers
- Lead replacement
- Lubricity enhancers
- Anti-foaming agents
- Anti-icing additives
- Biocides
- Anti-corrosion additives
- Cold flow enhancers (Bio-Diesel)
- Jet-fuel stabilizing additives
- Denaturing (Ethanol)
- Detergent additives
- Exothermic Additives
Additive pressurising systems
We specialise in the design and fabrication of pump skids for the pressurisation of additives, hydrocarbons and chemical liquids.
Pressurising pump skids ensure delivery of additive at sufficient differential pressure to allow effective injection into the main product line. Insufficient additive pressure can cause a number of problems including fluctuating treat rate which is costly and results in off-spec products.
By ensuring a sustained additive pressure, the function of the fuel additive systems is maximised, products are delivered on spec and expensive additive losses are avoided.
Most of our systems are built off-site in skid form and tailored to suit the specific application, be that pressurising a single additive or a fully integrated system to offload, store and pressurise an additive.
Our skids can be engineered to incorporate a host of options including:
- Single or dual/redundant pumps.
- Motor control and heating.
- Temperature monitoring. Flow monitoring.
- Pressure monitoring.
- Built in filtration/strainers.
- Provision for exothermic additives.
- Integrated offloading or loading.
- Integrated bunded storage with level monitoring.
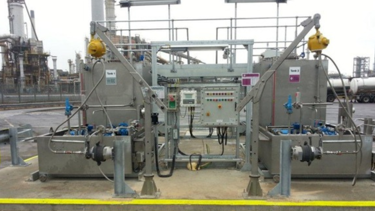
Additive pump skids are typically fabricated from stainless steel pipework on a galvanized steel frame. Through pump and motor selection we can accommodate a wide range of applications and treat rates. A standard configuration typically includes inlet ball valve, strainer, back pressure control valve, pressure relief valve, pressure gauge, outlet isolation ball valve, motor control centre with heaters and on/off/auto switches.
We select pumping technology appropriate to the application over and above any specific manufacturer allegiance.
Dual pumping technology
A unique feature of our dual pump skids is our optional proprietary pump-sequencer with optional handheld controller. The sequencer operates the pumps alternately, extending their life and building in redundancy which is vital in the event of a pump failure. The sequencer automatically starts the standby (redundant) pump should the main pump fail to build or maintain pressure.
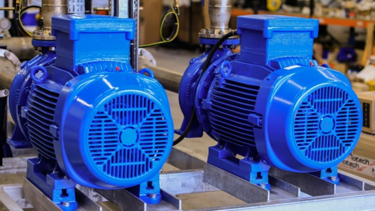
Additive injection systems
Standalone additive injection systems
Standalone systems are designed to inject one or more additives into a product line, typically using an injection block such as the Flotech FLOBLOCK which is controlled either by an on-skid controller or off-skid PLC or DCS. For larger injection rates, we use our compact piped injector design to provide higher flow rates without the need to significantly increase skid size.
The solutions we deliver are fully customised to suit our customers’ requirements in terms of additive injection rate, footprint and application. We also build stand-alone systems which incorporate additive storage in the ‘mother/daughter’ format.
Our ‘mother/daughter’ skids combine a stand-alone injection system with integrated bunded product storage and extended capacity in the form of an IBC. To fill the integral tank, an IBC is positioned on top of the skid which then gravity drains into the tank mounted on the skid below. This type of design helps avoid the chance of running the system dry and allows tank filling during loading.
We have designed systems which inject during loading and offloading of bulk fuels, as well as when filling and emptying individual vehicles. The projects we have undertaken cover a broad spectrum of applications, from injection of anti-icing additive into jet fuel to biocide treatment during the filling of bus fuel tanks.
Loading rack-mounted injection systems
The majority of fuel terminals make use of loading rack-mounted injection systems controlled by a site DCS, PLC or 3rd party controller such as an Accuload or Minpak. We are experienced in all of these systems and our service team maintain over 300 injectors in the field, as well as their respective controllers.
We have the ability to introduce additive injection to loading racks, modify existing systems and supply turnkey solutions including skid-mounted loading racks inclusive of additive injection as well as vapour recovery and blending.
Injectors are typically housed on a backplate or within an injection cabinet.
Turbine-driven Injection Systems (TDI)
The Flotech TDI delivers accurate self-powered additive injection, lending itself to installation in remote locations or where power is otherwise unavailable.
The TDI is fitted within the main product line and uses the power of the product flow to drive a turbine. The turbine then drives positive displacement injector heads via a gearbox. As the main product flow varies, the proportional change in speed of the turbine ensures that the rate of injection is adjusted accordingly.
The simple mechanical nature of these systems makes them inherently low maintenance.
You might also be interested in...
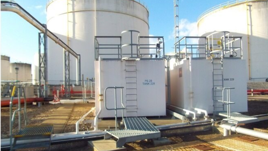
Containerised systems
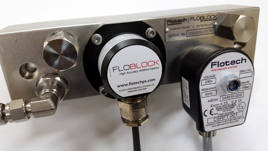
FLOBLOCK injector and sensor
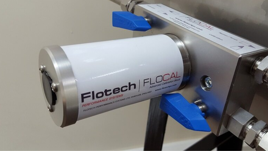
FLOCAL calibration device
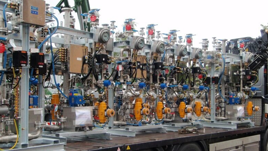
Blending solutions
Here to help with seamless delivery and management of your next process industry project.
Our experts are available to advise, support, and assist with any issues relating to your storage tanks and liquid process infrastructure ensuring you have a safe site, prevent any pollution, and remain operational.
Speak to our experts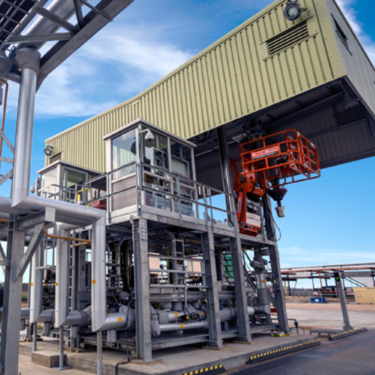