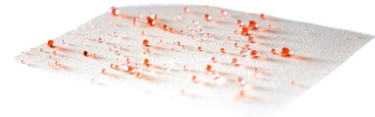
Advanced coatings
We are the UK distributors for GENTOO and Ultra-Ever Dry (UED), advanced hydrophobic and super hydrophobic coatings that can be applied to virtually anything to repel liquids and withstand abrasion.
The nano-coatings protect equipment, tools, buildings and other surfaces from corrosion, built-up of dirt, and contamination, helping to save money, improve safety and create a cleaner work environment.
We are at the forefront of driving this technology into commercial applications.
GENTOO hydrophobic coating
GENTOO is a dense polymer system that forms a barrier against corrosion initiators. This is due to its low surface energy, high density, and low porosity. The system is conformal, pinhole free, and very thin (4-6 microns) compared with traditional polymer coatings but far denser and more durable. The higher density of the system provides an excellent barrier to water and corrosive ions.
It has a number of benefits:
Adhesion and durability
GENTOO has robust adhesion to painted, plated, and bare metallic substrates, as well as glass and surface primed plastics. The coating has demonstrated excellent resistance to salt spray, UV exposure, and chemical exposure – significant improvements over traditional hydrophobic coatings. Testing and technical data is available upon request.
Corrosion resistance
When used on top of other qualified systems, GENTOO further reduces corrosion and extends the lifetime of the barrier system and therefore the coated substrate. This is due to its excellent water and salt shedding properties and impact resistance. These properties also significantly reduce the effects of galvanic corrosion of dissimilar metals.
Easy cleaning
The low sliding angle combined with the high dirt and solvent resistance of the coating allows for easy cleaning of many surfaces with less water.
FAQ's
GENTOO is a two-part coating that is mixed together and then applied as a single coat. It can be flow-coated, dip-coated, HVLP sprayed, or painted on with a brush or roller. It provides a lightweight, thin (4-6 microns) coating with minimal surface preparation.
GENTOO should be mixed in equal parts (1:1) of Part A and Part B by weight, not by volume for a minimum of 90 – 120 minutes, depending on temperature of surroundings, to hydrolyze the chemicals together and allow the proper reaction to occur. (see a video on how to check for hydrolysis).
Equal sized containers are sold in equal weights for Part A and Part B.
GENTOO can be cured in an oven at 90 °C (194 °F) for 1 hour or in ambient conditions for 24-48 hours. After application GENTOO is dry to the touch within 20-30 minutes. After 24 hours of curing at ambient conditions, if it is found to meet the needs of the customer, it may be put into service. Performance may improve after multiple days of curing at ambient conditions.
Yes. GENTOO has been tested with a wide range of solvents including mild soap, salt water, isopropyl alcohol (IPA), naphtha, some acids, heptane, jet fuel, deicing fluid, hydraulic fluid, lubricants, and others. The coating maintains its performance durability.
GENTOO hydrophobic coating is very durable so removing it is can be difficult.
GENTOO can be removed using abrasive materials such as heavy-duty Scotch Brite™ (which contains aluminium oxide). A chemical solution of 100% pure potassium hydroxide with 99% isopropyl alcohol may also be used. A recommended ratio is 1 lb (0.45 kg) of potassium hydroxide to 2-3 gallons (7.5 -11 litres) of isopropyl alcohol. Paint remover Eldorado PR-3500 (MIL-R-81294) may also be used to remove GENTOO.
Note: These removal methods may damage the substrate and/or coating beneath the GENTOO coating. Appropriate safety precautions, including the use of proper personal protective equipment, must be taken when removing GENTOO from a surface.
No, GENTOO does not contain silicone.
Longevity of the GENTOO coating will vary based on environmental factors, abrasion, chemical contact, etc. In general, it should last well beyond five years in an indoor environment with no abrasion. Outdoors, it is likely to last 3-5 years depending on the conditions and application. After long outdoor service, it has been observed that the sliding angle of liquids will tend to increase over time, but the coating will still be effective. GENTOO is a new product, developed under a number of military SBIRs (developmental grants) and there has been quite a bit of testing done, but there is still much to learn.
No testing has been performed on ultimate elongation, but GENTOO can be stretched. There is data for coatings on polyurethane that have been stretched to >1500% before breaking. Elasticity has not been tested. Elongation beyond 100% would not be elastic. A rubber primer/surface treatment may help adhesion.
GENTOO is an excellent anti-corrosion coating. GENTOO’s dense structure provides a high physical barrier to electrolytes that cause corrosion and an insulating electronic barrier for galvanic corrosion. For best results, a paint or another protective coating should be applied to the substrate, and then GENTOO should be applied when the paint or other coating is still “green” (tack-free but still has reactive groups available to help bonding). GENTOO hydrophobic coating can also be applied to a paint or other coating after it has dried, but surface roughening (if acceptable) is recommended to promote adhesion. GENTOO can also be applied directly to a substrate. In this case, surface roughening (if acceptable) and/or other surface preparation methods are recommended to promote adhesion.
We are looking at an option to be able to do this. It may require a light sanding or abrasion to allow better adhesion. We are working on a development to allow a “refresher spray” to be applied to the old coating to refresh the performance of the top surface.
Stretched acrylic, glass, aluminium, stainless steel, brushed steel, polycarbonate panels, wood, rubber, leather, polyethylene, painted surfaces.
It should help prevent build up because it is a durable hydrophobic coating, however, we do not have any testing to support this claim at this time. Real-world testing is recommended.
For plastics and acrylics, we recommend preparing the surface with a corona treatment and then wetting the surface with IPA prior to applying GENTOO. Corona treatment is not a requirement, but is a recommendation that may help achieve the best bonding of the GENTOO coating to the substrate. Flame coating of polyethylene plastic has also proven effective. Some plastics have not required any pre-treatment, so testing the need for pre-treatment on a specific plastic would be advised.
The initial coating exhibits a contact angle of approximately 110° - 115° for many liquids. The watershed angle is 5°- 10°.
We have test data showing GENTOO on metal being bent 180 degrees over a 1/8” diameter mandrel, without any cracking. The hybrid inorganic-polymer coating exhibits excellent flexibility.
GENTOO makes a great top coat – it has been coated on bare metal (aluminium, steel, stainless steel, etc.), on plating (Cd, Zn-Ni), and on top of current primer/top coats.
Yes, GENTOO can be applied with HVLP spray equipment (it can also be applied by flow coating, dip coating, brush, etc.).
The coating thickness is normally 4-6 microns, much thinner than a typical paint. The thickness is mainly controlled by viscosity of the solution, which is close to water viscosity. The coating can be thicker or thinner based on concentration, but we typically like to be between 1-10 microns.
There has not been much testing done showing corrosion resistance versus thickness of GENTOO, as it is difficult to build the thickness of GENTOO (versus a paint that can be built up over itself to achieve a targeted thickness). However, even a thin coating 4-6 microns) of GENTOO will help to prevent corrosion, since it is hydrophobic, and it is insulating and acts as a barrier.
There are no known chemical compatibility issues. The chemistry can be modified, if necessary for adhesion to alternative substrates, but would be good as is on glass, metals, and ceramics.
The coating is currently relatively high VOC, so there are some controls necessary for application.
It is named after an Antarctic species of penguin that repels water and oil off its feathered coat. Learn more. It is NOT short for “generation two”, as some have guessed.
Ultra-Ever Dry (UED) Super hydrophobic coating
UED uses proprietary omniphobic technology to coat a surface with patterns of geometric shapes that have “peaks” or “high points”. These high points repel water, some oils, wet concrete, and other liquids unlike any other coating.
UED has vastly improved adhesion and abrasion resistance, compared to previous super hydrophobic technologies, allowing it to be used in applications where greater durability is required.
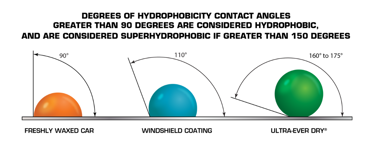
It has a number of benefits:
Anti-wetting
The superhydrophobic coating keeps objects dry - water and many other liquids are easily repelled.
Anti-corrosion
UED offers enhanced corrosion protection since the superhydrophobic coating repels water, saltwater, aqueous acids and bases.
Anti-icing
The superhydrophobic properties of UED keep coated materials completely dry, eliminating the formation of ice or, in the case of frost, making the removal of ice dramatically easier.
Anti-contamination
Water and other liquids that contain bacteria or radiation never actually contact the surface of the coated material so bacteria and radiation is greatly diminished or eliminated and the surface is easy to decontaminate. Dust and dirt are easily removed with low pressure water.
Self-cleaning
UED repels dirty water and some oils, and remains clean and virtually bacteria-free. When dust, dirt or other molecules accumulate on a superhydrophobic coated surface, a light spray of water or a blast of air grabs the dust and removes it.
Product life-extending
Many products fail from moisture, water, oil or simply getting too dirty for continued use. Use UED superhydrophobic coating to extend the life of electric motors by preventing the build up of moisture on the windings, coat nuts and bolts to prevent corrosion, coat tools, equipment, and virtually any item that needs to be kept dry, corrosion free, de-iced, uncontaminated or clean.
Commercial applications
Some of the many ways that Ultra-Ever Dry can be used:
- Clothing - Boots, footwear & PPE .
- Building material - Bricks, cinder/breeze blocks, concrete, timber, roofing materials.
- Electronics - Printed circuit boards, connectors, housings, motors.
- Tools, Equipment and hardwear.
- Vehicles - Cement trucks, lorries, loadbeds.
- General corrosion prevention.
- General protection from acids/bases.
FAQ's
The Ultra-Ever Dry® formula is susceptible to environmental conditions such as UV. This coating will offer approximately one year of outdoor life before recoating of the top coat would be required. When used in indoor or covered applications outdoors, the coating should last for a year or more. If the top coat has diminished due to environmental conditions, simply reapply the top coat to regain the superhydrophobic properties (assuming the bottom coat is still present). UED coating is also susceptible to abrasion.
The working temperature range for a coated surface is from -30°F to 300°F (-34°C to 149°C) once it has been applied. We would recommend further testing for any application that will be exposed to temperatures above 300 °F (149 °C). The coating should be applied at temperatures between 50°F to 90°F (10°C to 32°C).
Almost any material is a candidate for application: steel, aluminium, other metals, plastic, leather, fabric, wood, concrete, etc. The coating can be applied to and will bond to smooth surfaces. Preparing an already cleaned surface with heavy-duty scotch brite and/or sanding the surface with 320-800 grit sandpaper will improve adhesion. Ultra-Ever Dry® is not recommended for use on acrylics due to the high solvent content. Please note that the coating has a hazy translucent white appearance.
No UED is not available for consumers at this time.
Added value
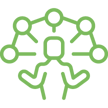
Technical expertise
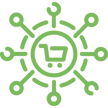
Product selection
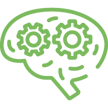
Knowledge
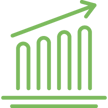
Proven results
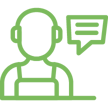
Support
Here to help with seamless delivery and management of your next process industry project.
Our experts are available to advise, support, and assist with any issues relating to your storage tanks and liquid process infrastructure ensuring you have a safe site, prevent any pollution, and remain operational.
Speak to our experts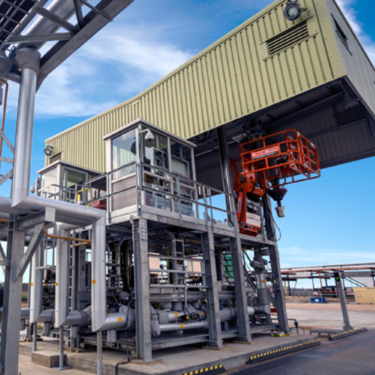