
Loading systems
We design and manufacture high-quality loading systems for the safe transfer of liquids and liquified gases.
Our skid-based solutions incorporate single or multiple loading arms and other features and are built to order to improve operator safety, reduce spills and minimise losses.
Our experienced engineers can build a system to suit your exact specifications.
- Flexible design.
- Wide variety of component options.
- System is engineered to suit the users current and future loading or offloading requirements.
- Skid-based solutions make the project cheaper, safer, and more convenient.
Added value
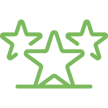
Industry-leading
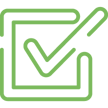
Product selection

Partners
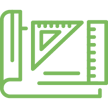
Design
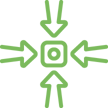
Compact
Our systems are built offsite in skid form. The advantages of this approach include:
- The system can be piped, cabled and flow tested in advance of delivery.
- Snagging is done off-site which minimises site assembly and start-up time.
- Large skids can be built in modular form to allow road transportation.
- Reduced time on site.
- All welding, assembly and testing is performed at our fully fitted facility in Hampshire by qualified and experienced personnel.
Bottom loading systems
We design and manufacture bottom loading skids for loading road tankers, rail tankers and ships. The fluids we work with include petrochemicals, beverages, pharmaceuticals and chemicals.
Our skids can be engineered to incorporate the following options as required:
- Single or multiple loading arms / connections.
- Vapour recovery.
- Fiscal metering.
- Meter proving functionality.
- Overfill protection.
- SIL interlocks.
- Integrated pressurisation.
- Pre-installed additive injection and/or blending.
- Vacant frame space for future expansion.
- Built-in hoists for removal of pumps and meters.
- Earthing / grounding.
- Temperature and/or pressure monitoring.
- Breakaway / emergency release couplings.
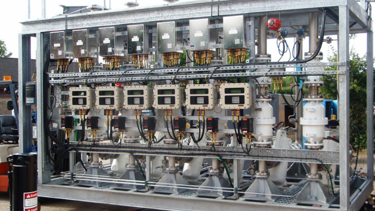
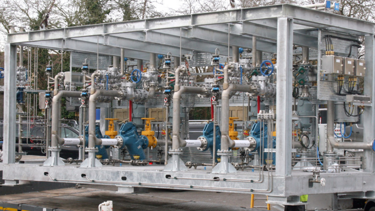
Top loading & offloading systems
We design and manufacture top loading skids for loading road and rail tankers. The fluids we work with include; petrochemicals, beverages, pharmaceuticals and chemicals.
Our skids can be engineered to incorporate the following options as required:
- Single or multiple loading arms / connections.
- Vapour recovery.
- Fiscal metering.
- Meter proving functionality.
- Overfill protection.
- SIL interlocks.
- Integrated pressurisation.
- Pre-installed additive injection and/or blending.
- Vacant frame space for future expansion.
- Built-in hoists for removal of pumps and meters.
- Earthing / grounding.
- Temperature and/or pressure monitoring.
- Breakaway / emergency release couplings.
Helicopter loading systems
We design and manufacture helicopter refuelling systems for a range of sectors including oil and gas (onshore / offshore), maritime and defence.
Typically, you will find our helicopter refuelling systems installed on offshore platforms, drilling rigs, FPSO’s, luxury yachts and offshore wind farms.
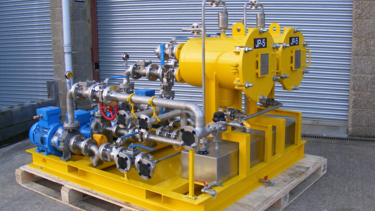
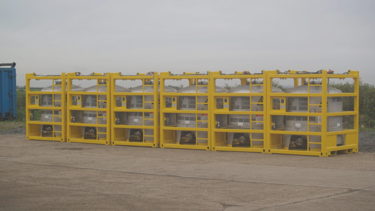
Our helicopter refuelling systems can be engineered to incorporate the following options as required:
- Storage tanks (transportable or static).
- Single or dual fuel pumps (electric, hydraulic or pneumatic).
- Control panel.
- Filter water separator.
- Air eliminator.
- Earth grounding system.
- Flow meter.
- Filter monitor.
- Hose reel and nozzle.
- Deluge systems (optional).
Tank specification
All of our offshore tanks are designed and built to pressure vessel standards (ASME VIII Div. 1 & PED 97/23/EC).
Manufactured with a double skinned tank to comply with CAP437, available in stainless steel or mild steel. All tanks can be painted to any specification and will be epoxy lined internally if made from mild steel.
We are able to design and build both static and transportable (TOTE) tanks. the transportable tanks will be manufactured inside a DNV2.7-1 transportable frame suitable for the transportation of hazardous goods offshore. Tank orientation within the frame can be either horizontal or vertical.
As a minimum all of our tanks will be manufactured with a manhole cover, inspection hatch, level measuring device and pressure/vacuum valves.
Pump specification
Our standard system comes with a duty/standby pump configuration with a flow rate of 225lpm and with a calculated pressure at the nozzle of around 2-3 bar.
We are able to supply API676 positive displacement pumps or centrifugal pumps, which can be driven by an electric, hydraulic or a pneumatic motor depending on the availability in the pumping location. Typically our pumps are mounted to an ATEX Zone 1 rated electric motor.
We will also protect the pump by means of flow switches and by putting an upstream strainer. Positive displacement pumps will also have a pressure relief valve that can either return to tank or back to the inlet depending on the installation.
A local MCC will be fitted on or near to the skid in an ATEX Zone 1 rated enclosure with either soft starts or direct on-line starters.
Dispenser specification
In most cases our dispenser would be fitted with a filter water separator, but this also can be located in the pump area. The filter water separator will be designed and built to ASME VIII Div. 1 pressure vessel standards and meet the Energy Institute (EI) standards EI 1596 and EI 1581.
At the nearest the point of refuelling (downstream of the flow meter) we will install a filter monitor. The filter monitor will be built to the same pressure vessel standards as the filter water separator and ensuring compliance to EI’s standards EI 1596 and EI 1583.
Both filter vessels will be fitted with a pressure relief valve, automatic air eliminator and a differential pressure gauge.
A flow meter with a high accuracy and repeatability will be fitted in the dispenser cabinet with either a mechanical or electrical register and a strainer air eliminator.
Hoses are designed and built to ISO 1825 and normally 1.5” in diameter, mounted on to a hose reel, which can either be manual, electrical, pneumatically or hydraulically rewound. A gravity (overwing) nozzle will come as standard with the option to have a pressure (underwing) nozzle as well.
Sampling points will be designed throughout the system but crucially there will always be one mounted in the dispenser to test and keep records of the fuel quality as per the Civil Aviation Authorities requirements when refuelling any aircraft.
All of our systems can be third party and PED certified.
You might also be interested in...
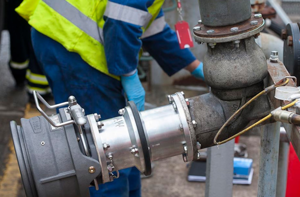
Couplers
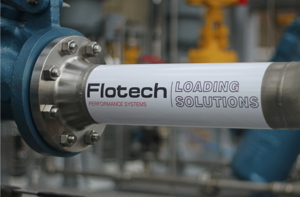
Loading arms
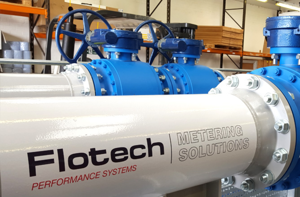
Metering systems
Here to help with seamless delivery and management of your next process industry project.
Our experts are available to advise, support, and assist with any issues relating to your storage tanks and liquid process infrastructure ensuring you have a safe site, prevent any pollution, and remain operational.
Speak to our experts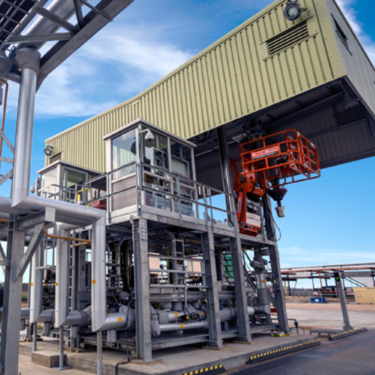